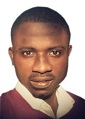
Okocha Stephen
University of Port Harcourt, Nigeria
Title: Harnessing conventional fuel production using solar-actuated pyrolysis reactor for waste plastics in developing countries
Submitted Date: 2018-09-04
Biography
Okocha Stephen is undergoing his PhD at the age of 29 years from the University of Port Harcourt under the African Centre of Excellence (ACE) scheme. He studied his masters under the center of Gas, Refining and Petrochemicals, UNIPORT and has his foundation as a Mechanical Engineer. He has been a researcher for\r\nyears helping in arresting the fuel scarcity in his country using Modular Refineries.His love for Energy has pushed him into researching on energy types, sustainable energy and the Oil/Gas industry. He has attended several conferences in Chemical Engineering which focuses on oil, Gas and Energy studies.
Abstract
It is estimated that only about 10% of the 9 billion tonnes of plastics being produced is being recycled. Its abandonment after use in the environment has enormously contributed to flooding, loss of aquatic lives and gives an unsatisfying look to the environment. In a means to sanitize the environment, polymer wastes undergo a series of recycling processes of which pyrolysis, which is the thermal conversion of plastics into conventional fuel without the presence of oxygen is being done. Although this very recommending, it requires a lot of energy to achieve which hinders developing countries from actively participating due to their low power generating\r\ncapacity. Hence, this paper looks at the possibility of performing the pyrolysis reaction of waste plastics in developing countries using the solar energy. The actuation was achieved by a concentrated radiation from the sun and backed up with flue Pyrolysis Gas when required. A process flow configuration which involves the reactor, solar lenses, vacuum pump, solar panel, inline components and the condenser is set up to perform the thermal gasification and condensation of waste plastics in the reactor. Computationally, finite element analysis (FEA) was done to see the thermodynamic effects inside and outside the reactor for effective pyrolysis oil production. Once successfully built, this will act as a model to aid environmental sanitation and the creation of jobs in developing countries.
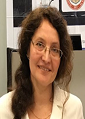
Anna Kapranova and Ivan Verloka
Yaroslavl State Technical University, Russia
Title: On the features of estimating the coefficient of inhomogeneity of a loose mixture during the operation of a gravitational device
Submitted Date: 2018-09-04
Biography
Anna Kapranova is the Head of Department of Theoretical Mechanics and Strength of Materials at Yaroslavl State Technical University, Yaroslavl, Russia.
Abstract
Statement of the Problem: The problem of assessing the quality of the resulting loose mixture does not lose its relevance due to the extensive use of mixing equipment in various industries. The main task of the technological operation of mixing granular materials is to obtain a homogeneous free flowing product. To successfully solve this problem, it is proposed to use a batch method of mixing loose components in a gravitational apparatus with additional mixing elements in the form of brush elements and inclined bump surfaces.\r\nIntroduction: The choice of the criterion for the quality of the mixture depends not only on the input parameters of the mixing process of the loose components (for example, physical properties of mixing materials), but also on the level of the theoretical base used in the development of engineering methods for calculating the appropriate apparatus. Such organization of the process of mixing granular components with rarefied streams with three mixing stages (τ = 1,nτ , nτ = 3 ) makes it possible to obtain mixtures with the ratio V1: V2 = 1: 10 or more. The study modeling of the quality criterion of the mixture is based on the theory of non equilibrium processes.\r\nThe purpose of this study: is to develop a method for estimating the coefficient of inhomogeneity of a loose mixture during the operation of a gravity\r\ndevice. Using the proposed stochastic model of the authors, it is possible to form a functional relationship between the coefficient of inhomogeneity\r\nof the free-flow mixture obtained at each of the three stages of portion mixing, with the design, regime parameters of the device and the physicomechanical\r\ncharacteristics of bulk materials. To implement the proposed mixing method, the condition must be met that in equal parts of the volumes of the granular mixture obtained at the previous stage and a new portion of the key component. To evaluate the degree of homogeneity of the finished product, an expression is proposed at each τ-stage linking the square of the average value of the volume fraction of the key component <Φτ >2 and the average of the corresponding square <Φτ 2 > Both quantities <Φτ 2 > , <Φτ 2 > are determined using the differential distribution function of the mixed components with respect to reflection angles from the bump surface, constructed on the basis of the theory of nonequilibrium random processes. As an example, the theoretical dependencies of the obtained grain size heterogeneity coefficients for natural sand and semolina at each mixing stage in a gravity apparatus. Here are denoted: ω - the angular velocity of the mixing drums; Δ - complex parameter of the apparatus reflecting the degree of deformation of the brush elements.\r\nResults: It is obtained that at a fixed value, effective mixing (the index KÑτ (Δ) has a minimum value) is achieved at practically identical angular\r\nvelocities of the drumω . An increase of every 0.05 units leads to a shift of the families of graphs to the left along the abscissa axis.\r\nConclusions: The results obtained depend on constructive-regime parameters of apparatus of gravity type, physic-mechanical properties of mixed\r\nmaterials. Results could be used as the basis for development of an evaluation method for the degree of homogeneity of the granular mixture in the\r\nengineering method of calculation of specified device parameters. The applied model operates with no equilibrium distribution functions for the\r\nnumber of particles by the characteristic parameters of the mixing process. The results of modeling the coefficient of inhomogeneity of the loose\r\nmixture allow us to choose rational ranges for changing the regime parameters of a new designed mixer and to develop an engineering method for\r\nits calculation.\r\n